Editor's Note: This post was originally published in December 2014 and has been updated for freshness, accuracy, and comprehensiveness.
Time-to-market, quality management, and compliance constraints are drastically reducing the amount of time a business has to manufacture products, making supply chain and material planning critical. With such a time crunch, the only way to succeed in the highly competitive market is to automate supply chain and material planning and integrate it into the core system that keeps a business running.
Using an ERP System
The best strategy for manufacturers in this situation is an enterprise resource planning (ERP) system, which can handle financial, operational, pricing, manufacturing, and fulfillment functions – just to start. Their assistance with supply chain and material planning techniques allows manufacturers of even the most complex products to make the time crunch manageable. ERPs also make it easier for manufacturers to anticipate customer needs and plan for them with greater accuracy, which results in fewer reworked orders and fewer back orders for customers.
Use these five strategies to streamline manufacturing and material planning performance with an ERP:
Real-Time Data
Strive to make material planning as real-time as possible. This ensures that forecasts are accurate and supply chains are optimized while also providing visibility across the entire manufacturing operation.
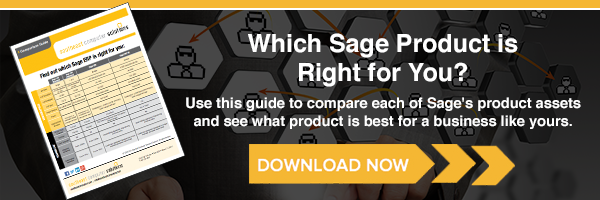
Integration
Supply chain and material planning systems should be tightly integrated into ERP, pricing, order management, and contract management systems. This ensures that production schedules match customer needs.
Agility and Stability
Material planning production workflows require both agility and stability. This ensures the highest quality product standards.
Analytics
Collecting and analyzing material planning system data minimizes unforeseen spikes in demand. This ensures a reduction in sourcing, procurement, and inbound inspection costs.
Mix-Mode Strategies
Mix-mode manufacturing strategies will become more commonplace, increasing the importance of supply chain and material planning and escalating as the scope of supplier relationships expand.
About Southeast Computer Solutions
Southeast Computer Solutions is based in Miami, Florida, and has additional operations in Mexico. For over 30 years, we have positively impacted the success of small and mid-sized businesses with effective business management implementations that improve our clients’ operations. We listen, we are accessible, and we care. Learn more by visiting our website or calling 305-556-4697.