Editor's Note: This post was originally published in November 2014 and has been updated for freshness, accuracy, and comprehensiveness.
Managing your inventory and your supply chain are important, but not always easy. Recent technological enhancements, however, can make managing your inventory and supply chain easier. In this case, the next software enhancement you should be considering is barcoding to improve shipping and receiving.
Why Barcoding?
Scanning inventory rather than keying it into the system as it enters your location speeds up the receiving process. When the order arrives at your warehouse, you need to do many things – scan the purchase order number, scan the items, do a count, and scan a specific lot or serial number. The faster and more accurately you do this, the better.
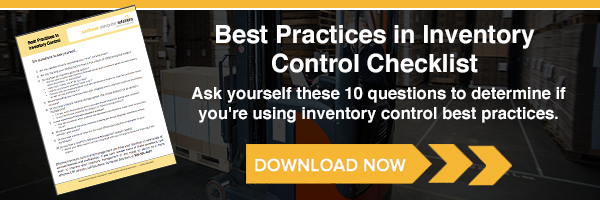
Getting a barcoding system that interfaces with your enterprise resource planning (ERP) system offers other advantages: it allows you to set up a transfer from one warehouse to another or, if you’d already received it in one warehouse, allows you to scan it a second time without altering your physical inventory count.
Additionally, when you have items with long lead-times and customers waiting to receive those items, barcoding allows you to cross-dock the inventory for rapid shipment. This means that instead of receiving the order into your receiving bin, you can receive it into a customer bin for a faster turn-around for the waiting client.
But What if Your Inventory Isn’t Barcoded?
If you want a barcoding system, but none of your inventory, or only some of your inventory, has barcodes on it, there is a solution: putting a barcode on the purchase order form. With this approach you can get a scan of the item even though the box doesn’t physically have a barcode label on it. A good barcoding system is smart enough to know that the items themselves didn’t have barcode labels, so when you receive 50 boxes of something, it will let you print 50 labels. You can then put a label on each box as you put it away and now your items are prepared for a physical count or the picking process for order fulfillment.
Implementing Barcoding
A barcode is not just a barcode. American markets have different barcodes than European markets, there are UPC codes and AM codes, and the barcodes used by UPS have nothing to do with the item that’s inside the box.
So as you consider barcoding to help with your inventory control, consider your inventory items and their current state. Do they have barcodes? If so, do they have barcodes that will work in the United States market? Also consider your warehouse layout, inventory management approach, and even staffing. How much would you have to change to get the positive effects of barcoding?
At Southeast Computer Solutions, we have the expertise to help you through the process of choosing, implementing, and utilizing a new barcoding system. Contact us today to see how we can improve your inventory control through barcoding.
About Southeast Computer Solutions
Southeast Computer Solutions is based in Miami, Florida, and has additional operations in Mexico. For over 30 years, we have positively impacted the success of small and mid-sized businesses with effective business management implementations that improve our clients’ operations. We listen, we are accessible, and we care. Learn more by visiting our website or calling 305-556-4697.