As we mentioned in last week’s blog, How Business Management Software Aids Food & Beverage Industry Compliance, product recalls can cost in the millions and take months to complete. And, despite the many precautions food and beverage companies take to avoid recalls, more than 20,000 people worldwide are still hospitalized due to foodborne illnesses.
The best way to avoid this is to put the focus back on supply chain traceability – that is, tracing a product's origin, its path through the manufacturing process, and to its ultimate destination.
Use these 3 strategies to ensure supply chain quality:
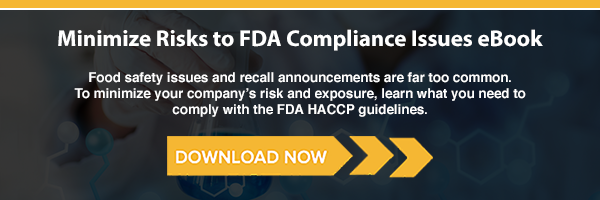
Manage Expiration Dates
The perishable nature of raw materials makes things a little tricky for food manufacturers. Closely monitoring expiration and best-by dates should be done in real time so manufacturers always know how fast a product needs to be moved or consumed. Doing so will maintain ingredient/product freshness for consumers' benefit as well as reduce waste for the manufacturer.
Focus on Quality
For a manufacturer, ensuring high quality across the supply chain is necessary for the health and well-being of their consumers, as well as for the health and well-being of their business. Tracking ingredients through every step of the production process minimizes the risk of a product recall and ensures that your products are free from toxins and contaminants.
Avoid Overstocking
Overstocking is nothing but lost money. While there is no denying that, as a food company, you deal with unpredictable supply and demand, overstocking increases the chances of food spoilage and, in turn, recalls. Inability to use the overstocked material within its stipulated time will put an entire production unit at risk of contamination. Therefore, avoid overstocking and using lean manufacturing, to save money and reduce waste.
How? With New Software
Food production is complicated. Managing the many facets of the complex supply chain requires a great deal of effort. As a small manufacturer or a start-up, spreadsheets and manual recordkeeping might seem like the easiest and most cost-effective manner to organize and maintain your business information. As your business grows, however, a comprehensive ERP system that keeps you on track by providing complete visibility over the entire manufacturing process and enables you to provide high-quality products to your consumers, will be the only solution.
Sage Enterprise Management (Sage X3)
A powerful business management solution like Sage Enterprise Management with built-in process manufacturing and accessible business intelligence can support your food and beverage manufacturing company by providing you with vital information for making important business decisions faster. The software’s robust core functionality allows you to streamline compliance and eliminate inefficiency, providing a significant advantage over legacy systems and other, less powerful ERPs.
Contact Southeast Computer Solutions for more information about getting an ERP system for YOUR food and beverage company.
# # #
About Southeast Computer Solutions
Southeast Computer Solutions is based in Miami, Florida, and has additional operations in Mexico. For over 30 years, we have positively impacted the success of small and mid-sized businesses with effective business management implementations that improve our clients’ operations. We listen, we are accessible, and we care. Learn more by visiting our website or calling 305-556-4697.